One summer when I was too inexperienced an engineer to find a real internship, I ended up with a volunteer position working at a non-profit working under a Nicaraguan engineer. Needless to say, the summer was an eventful one and I have many good memories and stories from that summer. One of my favorite projects was the design and construction of the “bicitrilladora”.
Some Background
The Nicaraguan non-profit I was working for was set up to improve access to healthcare for extremely rural communities. The villages they served were very hard to get to, often requiring multiple days of travel involving 4x4 trucks, Cessnas and dugout canoes. Conversely, the villagers could expect delays, substantial risk and great personal expense to get their products to market.
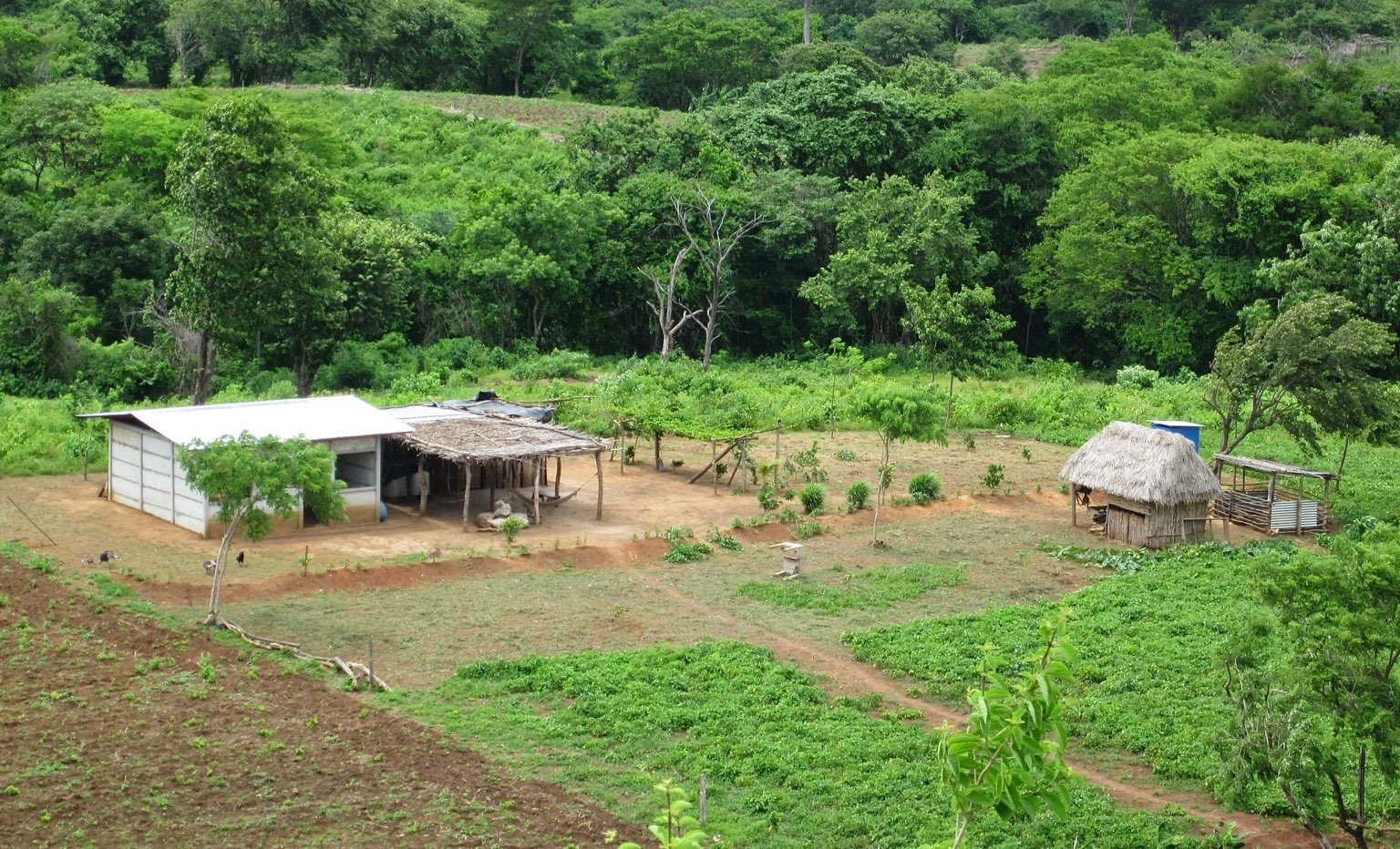
A photogenic rural family homestead in Nicaragua
The organization I was working for had observed that their best attempts to improve healthcare access would have only marginal impact unless they also worked to address some of the underlying reasons for why these villages were unable to get treatment. One of the most significant factors at play was that many people simply could not afford even the most subsidized healthcare treatment. An improvement in the economic prospects of a community would translate directly into better access to healthcare for that community.
Due to its stable shelf-life, the most common export from a village is rice. Before it can be cooked, rice must be dehulled. Dehulled rice is more valuable by weight, so my organization decided to invest some R&D in dehulling technology that might be feasible in a rural community. A successful technology could significantly improve a farmer’s profitability and, consequently, healthcare.
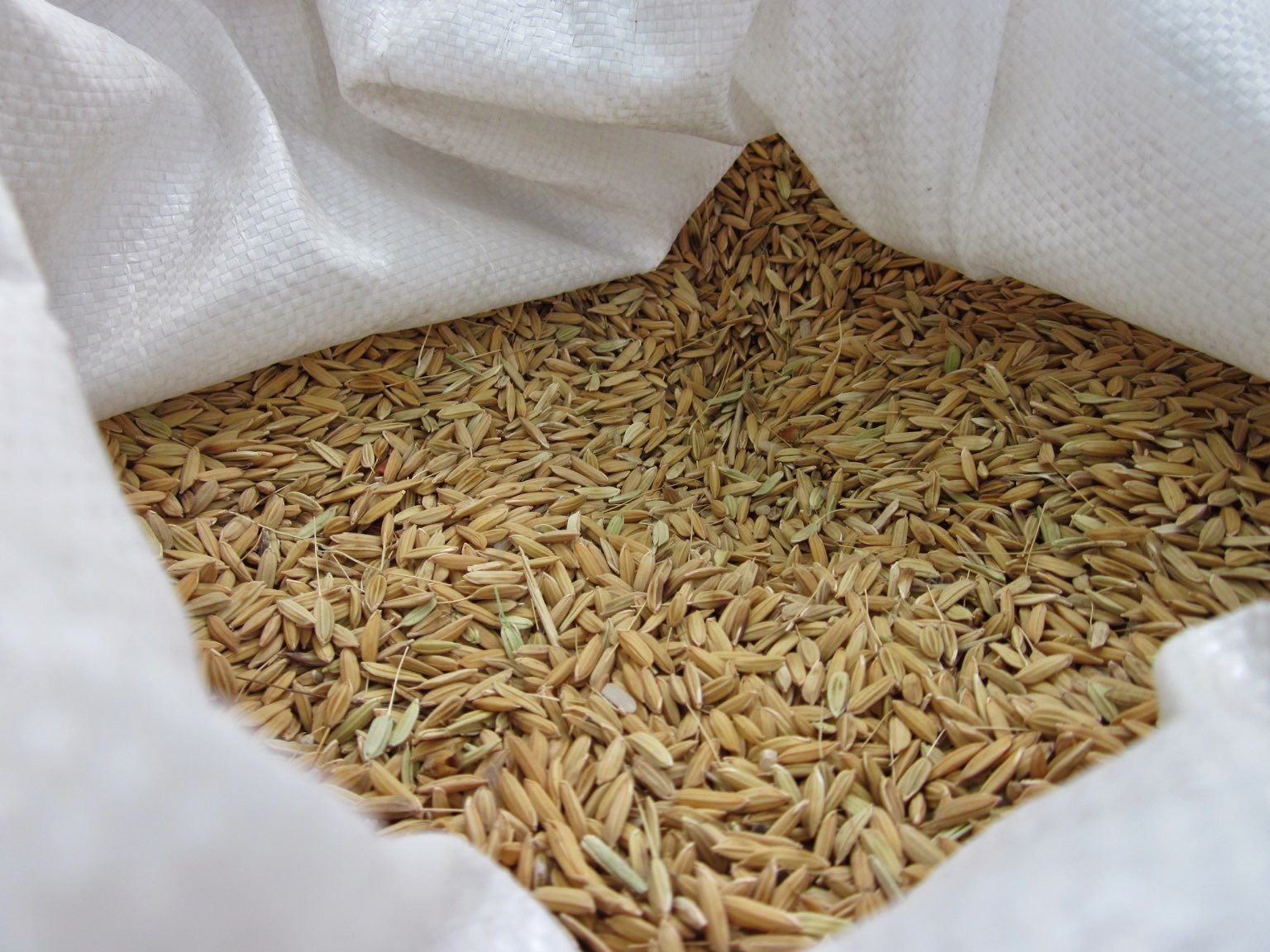
A sack of rice before it is dehulled.
A Prototype
Some villages are not so far from a road or major river and can bring in gasoline to run a generator occasionally. Others are limited to a community solar panel to charge a cell phone or a pocket radio, or import power in the form of AA batteries purchased downriver. Human power, on the other hand, is readily available.
For small batches of rice, such as for a family meal, it is possible to dehull rice with a large mortar and pestle, but this ancient tool is unsurprisingly too slow and exhausting for a farmer to process even their small yields, which are measured in 25 kg sacks.
But what if we somehow attached a small commercial rice dehuller to a set of bike pedals? A reasonably fit human can produce a steady 100 W for one hour on a bicycle, this was tantalizingly close to the lower power limit on the smallest commercial rice dehuller we could buy in town. Could we harness human power to dehull rice efficiently? To answer the question, I was to work on a prototype.
The construction and design of the prototype can be seen in the following photos.
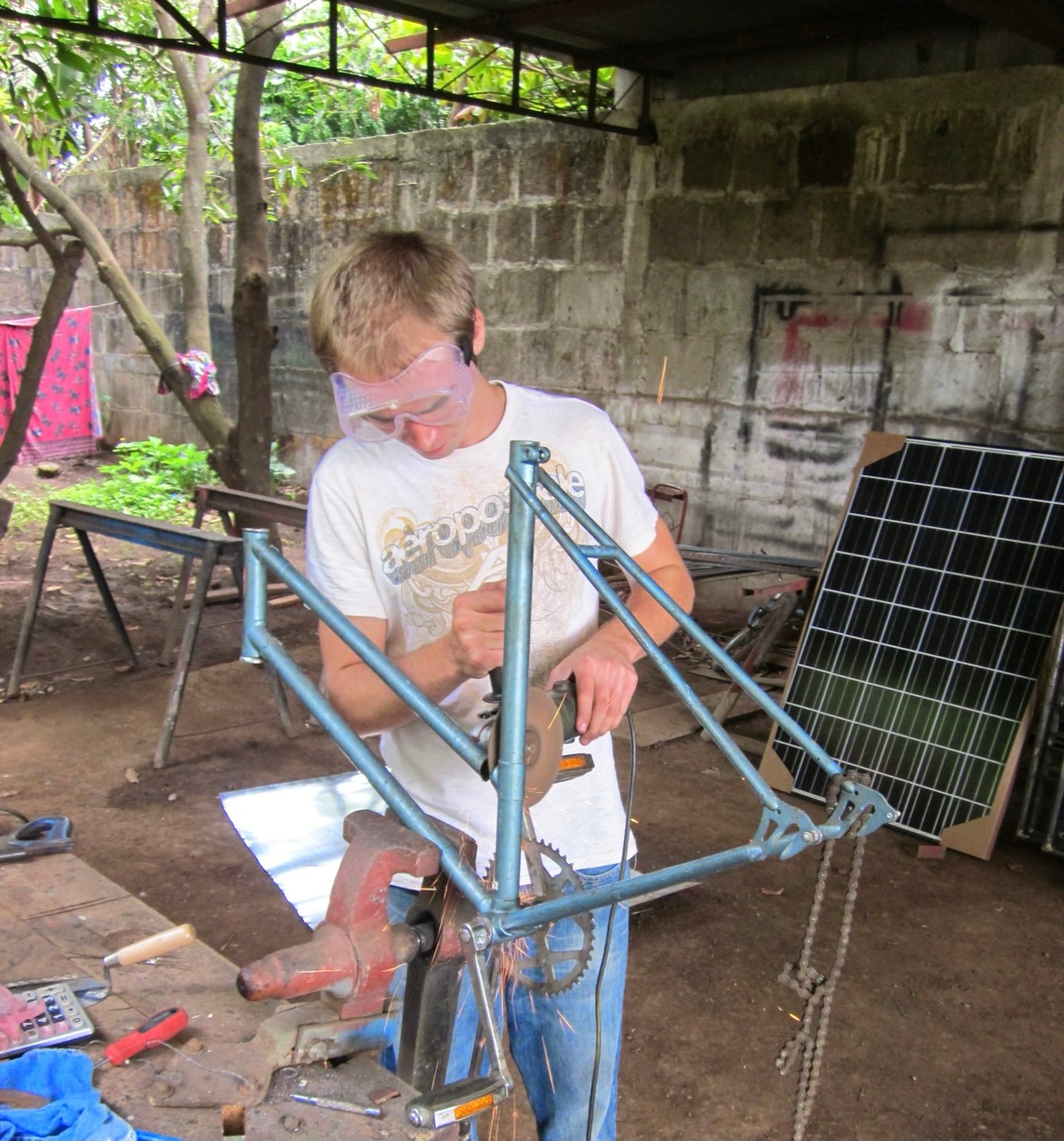
Sacrificing a bike frame to extract the crankset and seatpost
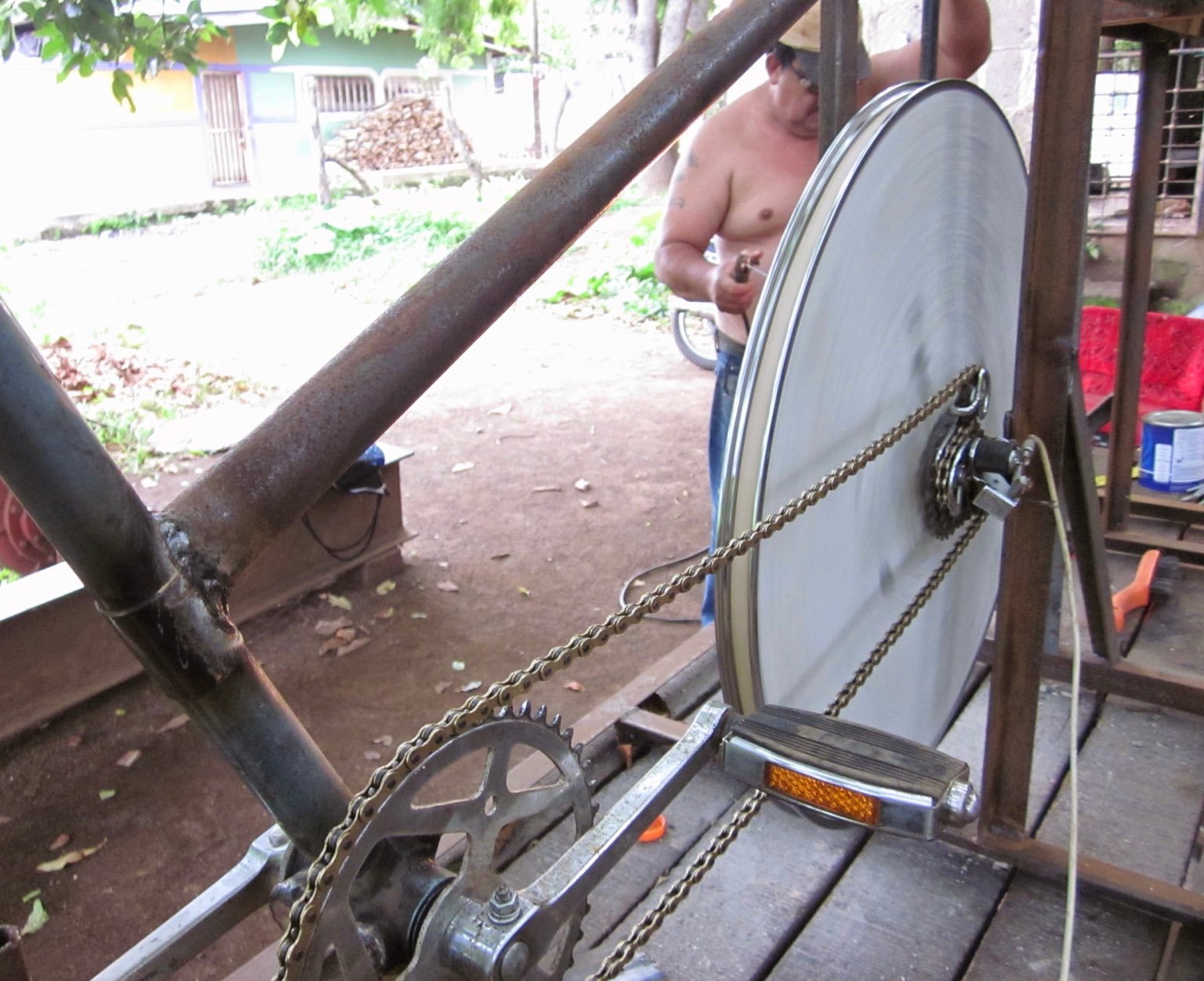
A flywheel is constructed by filling the rear wheel with concrete and is mounted ahead of the cranks. The rear derailleur is preserved. In the background, the shop owner casually finishes up some welds.
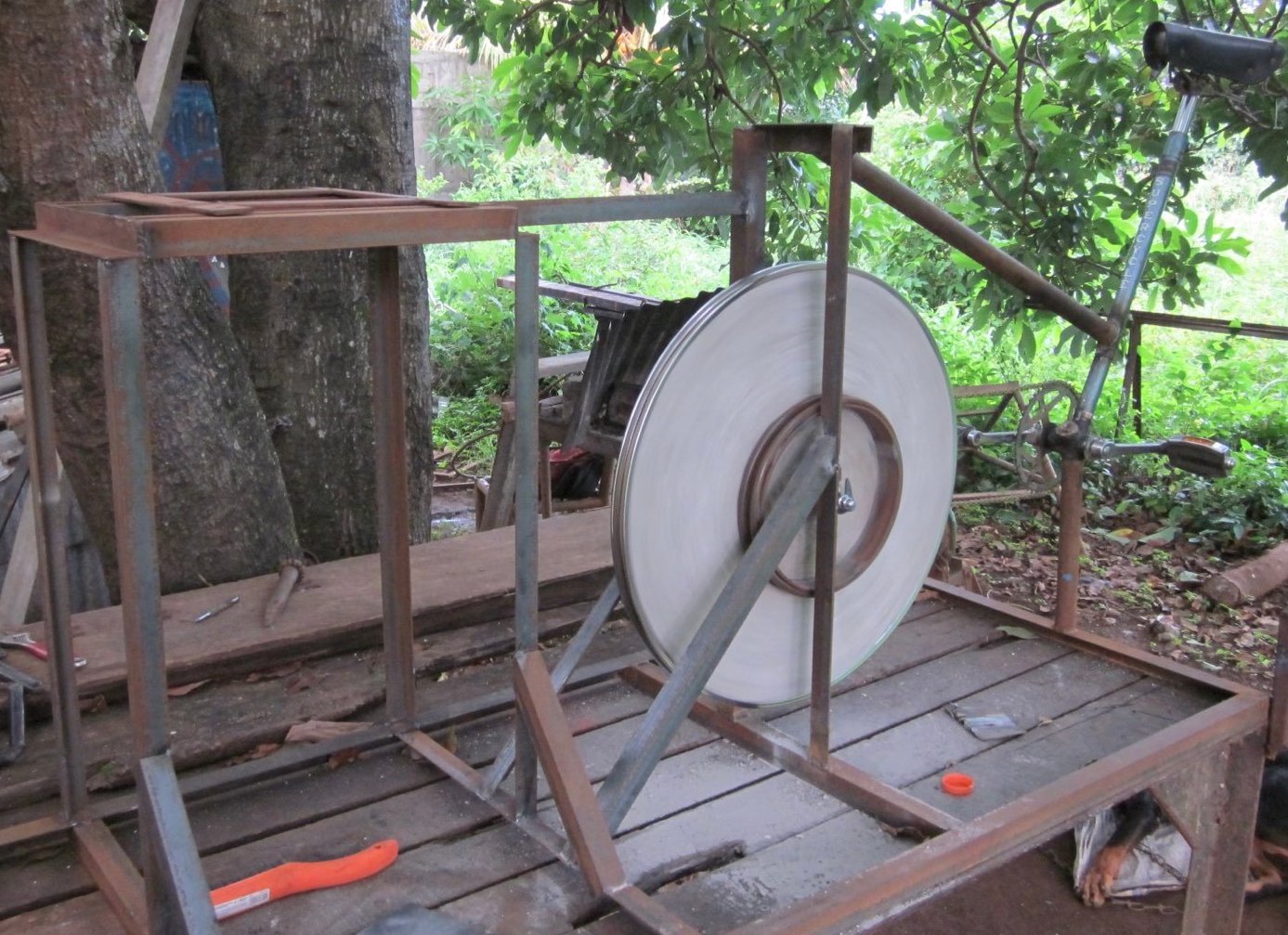
On the other side of the flywheel, a pulley is embedded into the concrete. This will be used to transfer power from the flywheel to the dehuller.
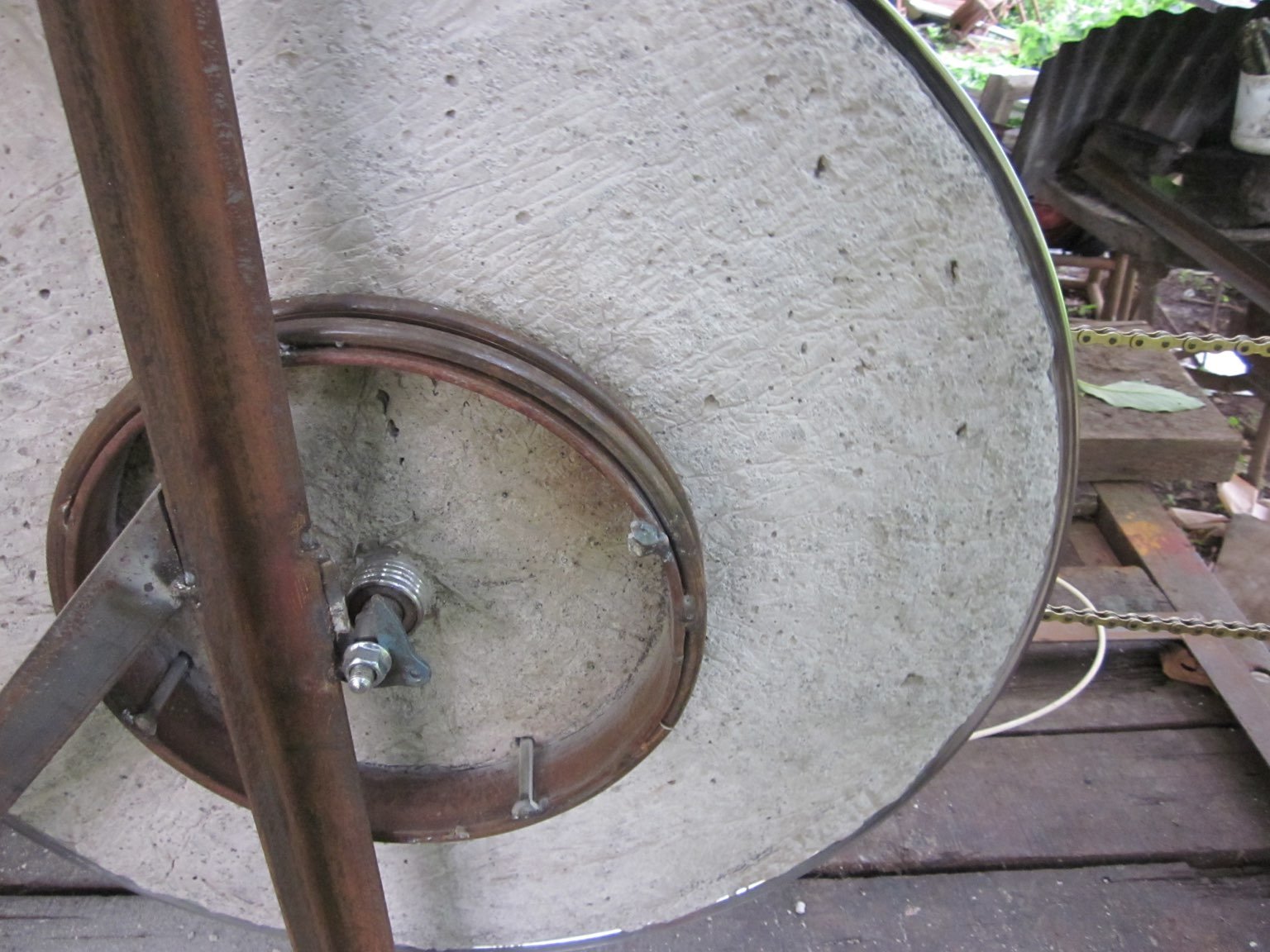
A closeup of the flywheel and the home-made pulley.
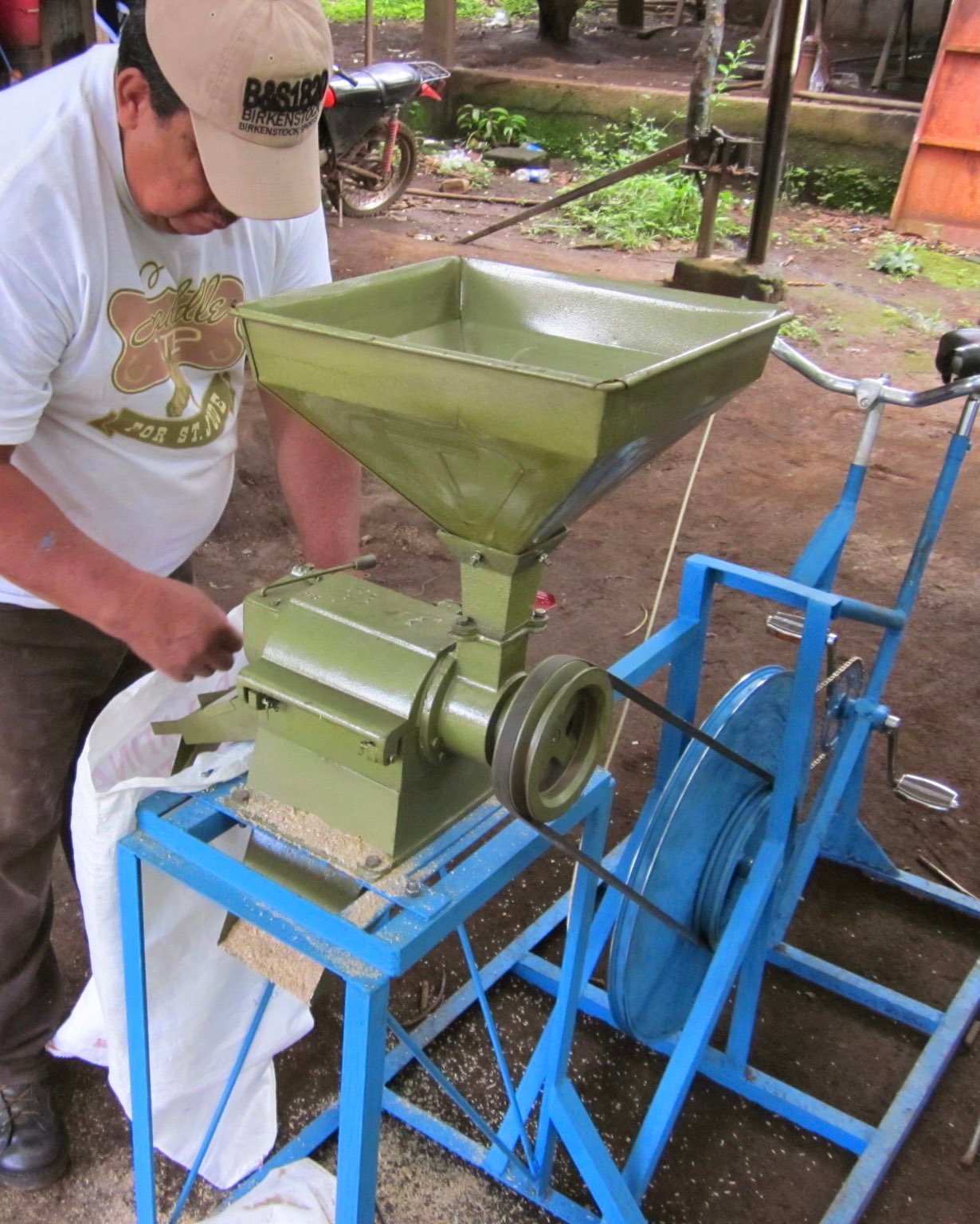
Painted and fully assembled, with the commercial dehuller mounted. The dehuller mount is slotted to set the belt tension. Unprocessed rice goes into the hopper at the top and out the shute on the side into the sack.
Results
Once assembled, the prototype was delivered to a rural community for testing. A lot of people enjoyed using the machine, almost equally as a way to show off how fast they could pedal as to extract the rice itself. Pedalling the bicitrilladora was not at all unlike spin class, and a few operators would be able to process a sack of rice in under two hours, much faster and easier than the traditional method.
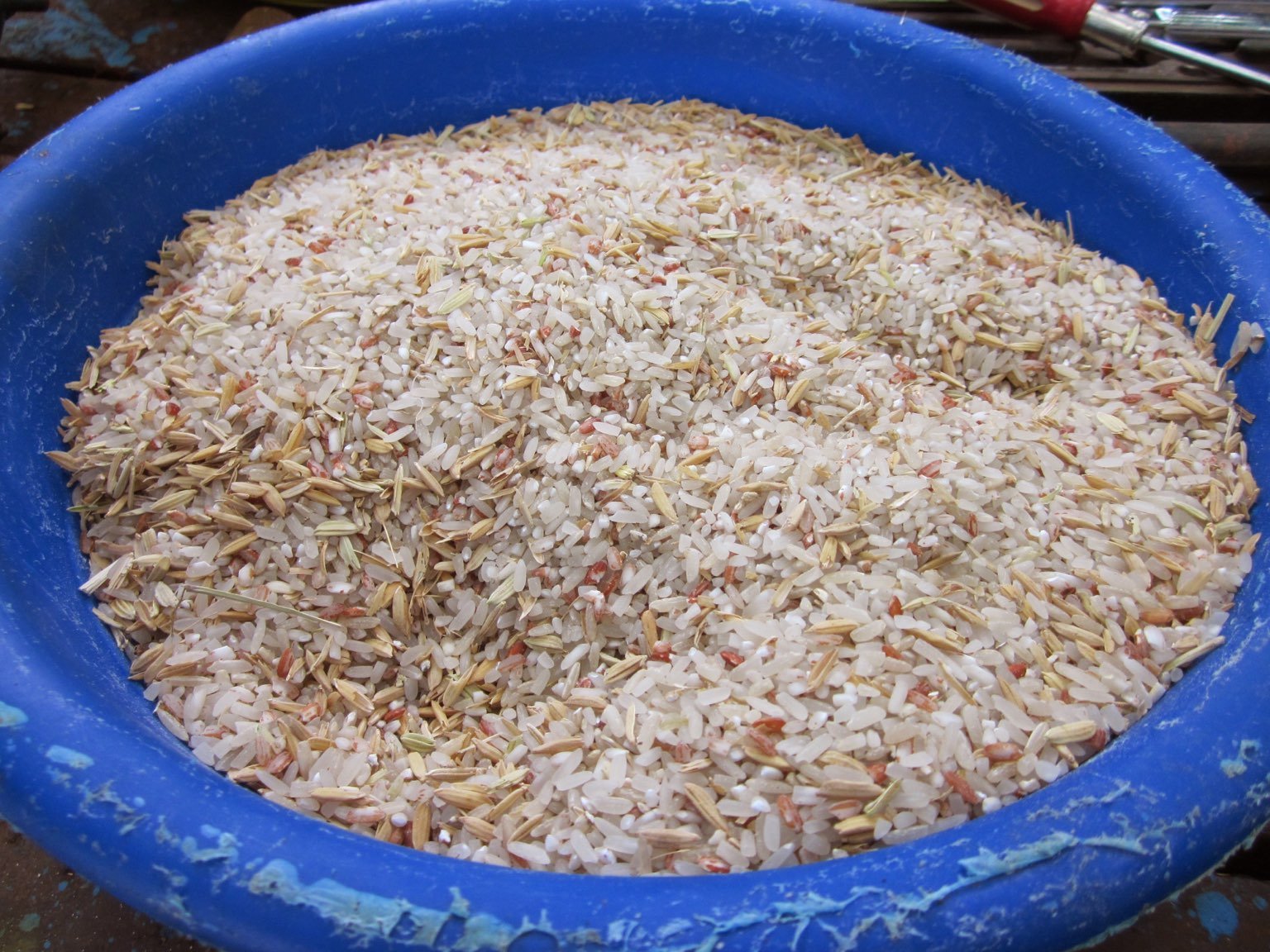
Rice from early in testing.
It took a bit of practice to operate the dehuller itself. Common issues were broken grains and grains still in the hull, as seen in the picture. Ultimately, I don’t think any more of this machine was made, however in my mind the limiting factor was not the pedal-power but rather the rather finicky commercial dehuller that we were using. Even so, the bicitrilladora was still viewed as preferable by many users over the traditional pounding method.